Rozwój inżynierii materiałowej a także technik wytwarzania przyczynił się w skali globalnej do zmian w stylu życia współczesnych ludzi. Jednym z jego przejawów jest możliwość szybkiego przemieszczania ludzi i ładunków w obrębie kontynentu i przestrzeni transkontynentalnej.
Wzrost wymiany osobowej i towarowej środkami masowego transportu generuje potrzebę energooszczędnego wytwarzania pojazdów, spełniających współczesne oczekiwania, zwłaszcza w zakresie zużycia paliwa i emisji gazów cieplarnianych do atmosfery. Jednym ze sposobów realizacji tych celów jest wzrost udziału lekkich materiałów polimerowych i kompozytowych w budowie pojazdów. Tworzywa polimerowe, mimo ostatnio pojawiającym się doniesieniom (często jako fałszywe wiadomości ang. fake news) o ich negatywnym oddziaływaniu na środowisko naturalne i człowieka, są materiałami dzięki którym można kreować przełomowe dla jakości naszego życia wynalazki. Przykładem jest opatentowany w 1870 roku celuloid, który umożliwił zapis ruchomych obrazów na taśmie filmowej i spowodował rozwój fotografii. Skuteczne ocieplanie budynków materiałami izolacyjnymi, wytwarzanie olbrzymich łopat wirników siłowni wiatrowych (w 2019 roku ich długość przekroczyła już 100 m) czy też skonstruowanie tzw. sztucznego serca (w tym również polskiego, autorstwa pracowników Fundacji Rozwoju Kardiochirurgii z Zabrza) do wspomagania pracy naturalnego układu krążenia pacjenta, nie byłoby możliwe bez udziału tworzyw polimerowych. Zasadniczym składnikiem w budowie tych materiałów są makrocząsteczki, które oddziaływują na siebie siłami wiązań chemicznych (najmocniejsze, wiązanie pomiędzy makrocząsteczkami w wyniku sieciowania makrocząsteczek – duroplasty) lub siłami wiązań fizycznych, głównie poprzez oddziaływanie międzycząsteczkowe van der Waalsa (tworzywa termoplastyczne). Termoplasty można wielokrotnie przetwarzać, ponieważ większość z nich ulega topnieniu w zakresie 200-300 stopni Celsjusza. Jedynie materiały o strukturze usieciowanej (np. żywice epoksydowe i poliestrowe, poliuretany, guma) nie topią się, co utrudnia ich wtórne wykorzystanie.
Przykłady lekkich konstrukcji:
Pas przedni do mocowania świateł w samochodzie ciężarowym
z poliamidu 6, z dodatkiem włókien szklanych (PA6 GF)
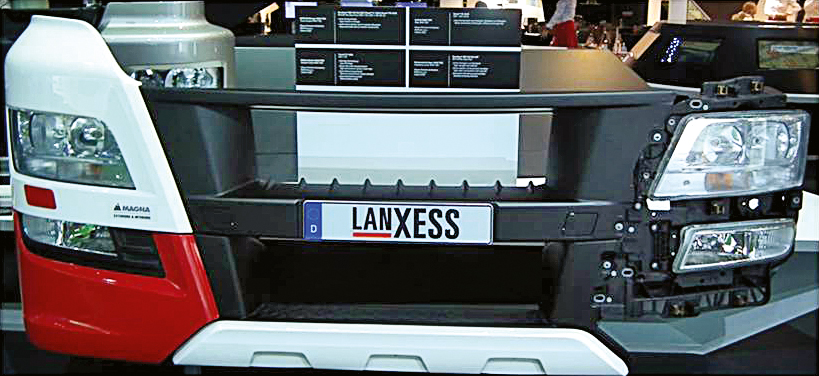
Karoseria samochodu i szyby wykonane z poliwęglanu (PC)
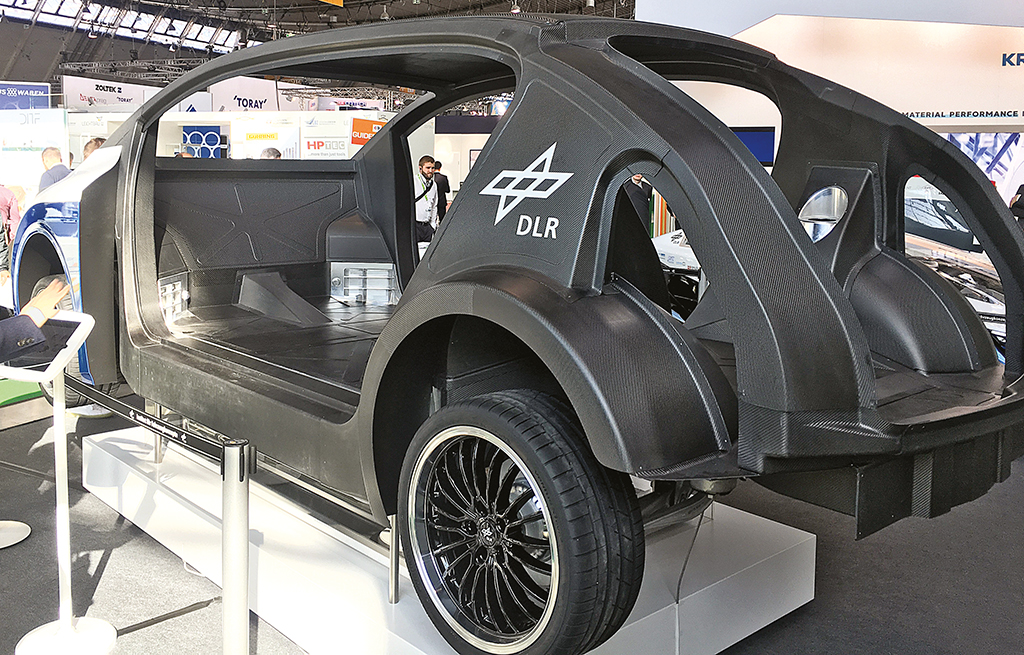
Wzrost wymiany osobowej i towarowej środkami masowego transportu generuje potrzebę energooszczędnego wytwarzania pojazdów.
Niewątpliwą zaletą tworzyw polimerowych jest ich mała gęstość od 900 do 2200 kg/m3, co w porównaniu do stali jest wartością wielokrotnie mniejszą (zakres gęstości stali 7400-7900 kg/m3). Ponadto, produkcja wytworów polimerowych
i ich recykling mechaniczny są procesami energooszczędnymi w stosunku do przeróbki innych materiałów konstrukcyjnych. Bardzo ważna z punktu widzenia użytkownika jest także ich dobra izolacyjność cieplna i elektryczna i dla i dla większości z nich hydrofobowość. Niestety tworzywa polimerowe posiadają wady, do których z punktu widzenia zastosowań w środkach transportu należy zaliczyć: niskie w porównaniu ze stalą i aluminium wartości modułu Younga oraz wytrzymałości statycznej i zmęczeniowej, zmienność właściwości mechanicznych w zależności od czasu obciążania i temperatury otoczenia, relaksacja naprężeń czy też kilkukrotnie większa w stosunku do stali rozszerzalność termiczna oraz palność. W związku z tym tworzywa polimerowe modyfikuje się napełniaczami wzmacniającymi, przede wszystkim włóknami ciętymi i długimi oraz uniepalniaczami.